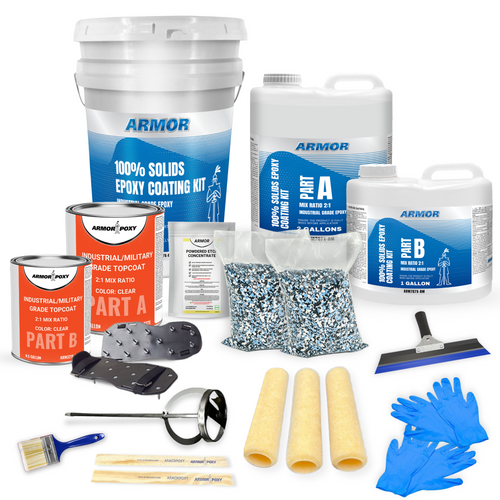
Epoxy Indoor Floor
ArmorPoxy takes your indoor floors to the next level with professional-grade epoxy and coating systems built for durability, performance, and style. Whether you're refreshing your basement, upgrading a workshop, or enhancing a commercial space, our solutions offer long-lasting protection and stunning finishes far beyond what traditional floor paint can provide.
ArmorPoxy makes it easy to achieve beautiful, reliable results—no matter your project size or skill level.
Products
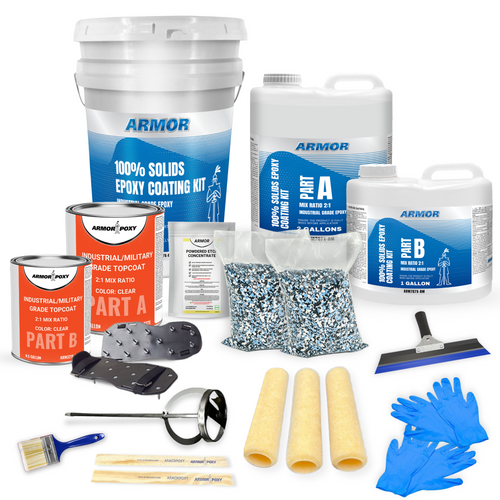
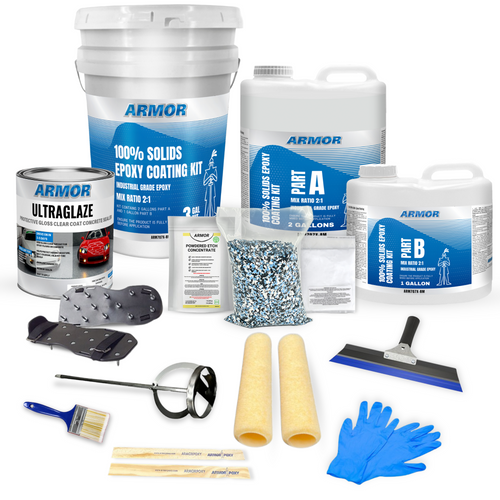
ArmorClad Epoxy Kit - Medium Broadcast - 300, 600, 900, 1200 Sq Ft Kit
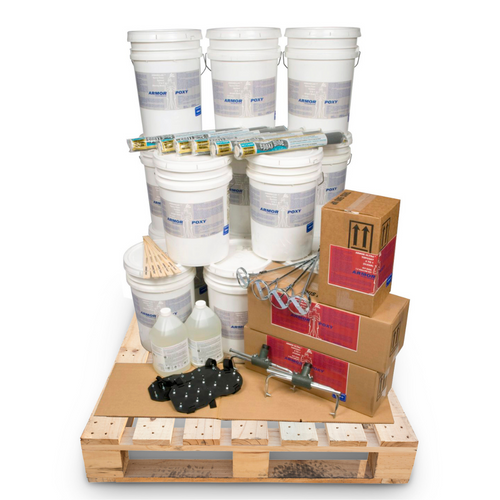
Job on a Pallet - Commercial Epoxy System - ArmorPoxy II 2-Layer - Per Sq Ft - Low & STD VOC
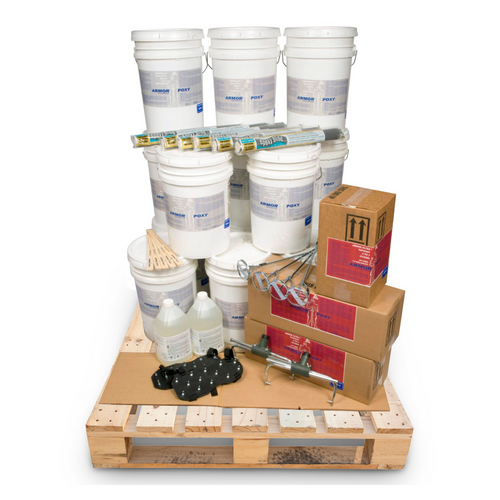
Job on a Pallet - Commercial Epoxy System - ArmorUltra 3-Layer - Per Sq Ft - Low & STD VOC
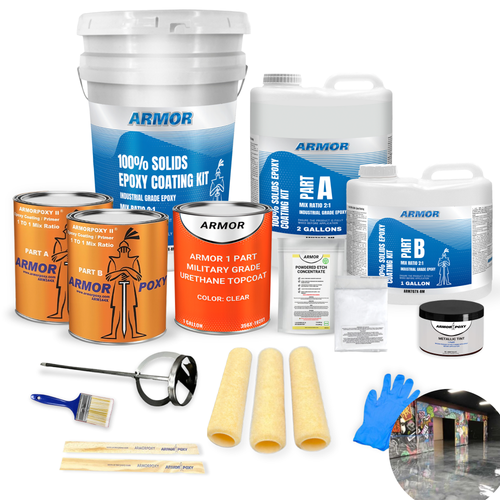
ArmorTallic Metallic Epoxy Complete Floor Kit 100% Solids Epoxy
Transform Your Indoor Spaces with Professional Floor Coating Solutions
When it comes to protecting and beautifying your indoor concrete surfaces, selecting the right coating system makes all the difference. Whether you're looking to upgrade your basement, workshop, or commercial space, understanding the various options available will help you make an informed decision that delivers lasting results.
At ArmorPoxy, as a leading provider of high-performance floor coating solutions, we offer everything from basic protective systems to advanced decorative finishes. With decades of experience in the industry, we've helped thousands of customers achieve professional-grade results in their indoor spaces.
What Makes ArmorPoxy Coatings Superior?
ArmorPoxy coatings are formulated with advanced chemistry that provides superior performance characteristics. Our products feature high-solids content, meaning more of the applied material remains on the surface after curing, resulting in a thicker, more durable finish.
The key advantage of our systems lies in their versatility and performance. Unlike single-component paints, our multi-component systems cure through chemical cross-linking, creating a tough, resilient surface that can withstand heavy use, chemical exposure, and temperature fluctuations.
Our coating systems are designed to work together as complete solutions. Each component serves a specific purpose, from primer adhesion to topcoat protection, ensuring optimal performance throughout the system's lifespan.
Transform Your Indoor Spaces with Professional Floor Coating Solutions
When it comes to protecting and beautifying your indoor concrete surfaces, selecting the right coating system makes all the difference. Whether you're looking to upgrade your basement, workshop, or commercial space, understanding the various options available will help you make an informed decision that delivers lasting results.
At ArmorPoxy, as a leading provider of high-performance floor coating solutions, we offer everything from basic protective systems to advanced decorative finishes. With decades of experience in the industry, we've helped thousands of customers achieve professional-grade results in their indoor spaces.
What Makes ArmorPoxy Coatings Superior?
ArmorPoxy coatings are formulated with advanced chemistry that provides superior performance characteristics. Our products feature high-solids content, meaning more of the applied material remains on the surface after curing, resulting in a thicker, more durable finish.
The key advantage of our systems lies in their versatility and performance. Unlike single-component paints, our multi-component systems cure through chemical cross-linking, creating a tough, resilient surface that can withstand heavy use, chemical exposure, and temperature fluctuations.
Our coating systems are designed to work together as complete solutions. Each component serves a specific purpose, from primer adhesion to topcoat protection, ensuring optimal performance throughout the system's lifespan.
Why Choose Professional Floor Coatings Over Traditional Paint?
The difference between professional floor coatings and standard paint applications is substantial. Traditional basement floor paint typically lasts only 1-2 years before showing signs of wear, peeling, or failure. Professional coating systems, when properly applied, can provide decades of protection and beauty.
Standard basement floor paint products lack the chemical resistance, adhesion properties, and durability needed for high-traffic areas. They also require frequent reapplication, making them more expensive in the long run. Professional coatings bond chemically with the concrete substrate, creating a permanent protective barrier that won't peel or chip under normal use.
Many homeowners initially consider basement floor paint as a budget-friendly option, but quickly discover its limitations. The thin film build of typical basement floor paint cannot withstand moisture, chemicals, or heavy use common in basement environments.
Understanding Different Types of Indoor Floor Coatings
Epoxy-Based Systems
Epoxy systems remain the gold standard for indoor floor applications. These floor painting epoxy solutions provide excellent adhesion, chemical resistance, and durability. The two-component nature of epoxy allows for precise control over working time and final properties.
Modern floor painting epoxy formulations have evolved significantly from early versions. Today's products cure harder, last longer, and provide better chemical resistance than ever before. They're particularly well-suited for basements, workshops, and commercial spaces where durability is paramount.
The thickness achievable with floor painting epoxy systems also makes them ideal for covering minor surface imperfections. A properly applied epoxy coating can hide small cracks, stains, and surface irregularities while providing a smooth, professional appearance.
Floor painting epoxy applications offer superior performance compared to traditional paints, with advanced formulations that resist chemicals, abrasion, and moisture. These systems create a protective barrier that maintains its integrity under demanding conditions.
How Do I Choose the Right Coating for My Project?
Assessing Your Environment
Consider the typical activities that will occur on the floor. Heavy equipment, chemical exposure, and thermal cycling all impact coating selection. Basement environments, for example, may experience humidity fluctuations that require specific system characteristics.
Traffic patterns also influence coating choice. Areas with heavy foot traffic need different properties than spaces primarily used for storage. Understanding your specific requirements helps narrow down the best options.
Performance Requirements
Chemical resistance requirements vary significantly between applications. A basement workshop may need resistance to oils and solvents, while a commercial kitchen requires different protective properties. Identifying potential exposure helps determine the appropriate system.
Temperature requirements also matter. Some applications may experience temperature extremes that require specialized formulations. Most indoor applications operate within moderate temperature ranges, but extreme conditions need special consideration.
What Are the Featured ArmorPoxy Products?
ArmorClad Epoxy Kits
ArmorClad represents our premium epoxy indoor floor coating solution. These kits include everything needed for professional results, from primer to topcoat. The system is designed for ease of application while delivering commercial-grade performance.
The ArmorClad epoxy indoor floor system features high-build characteristics, allowing for single-coat application in many situations. This reduces labor time while ensuring adequate film thickness for long-term protection. The system also includes decorative options like color flakes and metallic effects.
Each epoxy indoor floor kit is sized for specific square footage, eliminating guesswork in material ordering. The components are pre-measured and quality-tested to ensure consistent results. This attention to detail helps ensure project success even for first-time users.
ArmorClad epoxy indoor floor coatings provide superior adhesion and durability compared to traditional basement floor paint alternatives. The advanced chemistry creates a permanent bond with concrete substrates that won't peel or delaminate over time.
Job on a Pallet Solutions
For larger projects or contractors handling multiple jobs, our Job on a Pallet offerings provide economy and convenience. These packages include volume pricing, making them ideal for commercial applications or contractors working on several projects.
The pallet approach also ensures product consistency across large installations. All materials come from the same production runs, eliminating color or performance variations that might occur with separately purchased components.
Logistics are simplified with pallet shipments, reducing freight costs and ensuring all materials arrive simultaneously. This is particularly valuable for time-sensitive projects where delays can be costly.
ArmorTallic Metallic Systems
ArmorTallic represents our premium decorative floor painting epoxy solution. These systems create stunning metallic effects that rival expensive alternatives while providing superior performance characteristics.
The metallic floor painting epoxy systems use special pigments that create depth and movement in the finished surface. Each installation is unique, with patterns and effects that cannot be replicated. This makes ArmorTallic ideal for high-end residential and commercial applications.
Despite their decorative nature, ArmorTallic floor painting epoxy systems maintain the performance characteristics expected from professional coatings. They provide excellent chemical resistance, durability, and ease of maintenance while delivering exceptional beauty.
How Should I Prepare My Surface for Coating?
Proper surface preparation is critical for coating success. The concrete must be clean, dry, and properly profiled to ensure good adhesion. Cutting corners on preparation is the leading cause of coating failure, whether you're applying basement floor paint or professional epoxy systems.
Surface Cleaning
All contaminants must be removed from the concrete surface. This includes oil stains, paint, sealers, and any other materials that might interfere with adhesion. Different contaminants require different removal methods, and this process is especially important when upgrading from failed basement floor paint.
Oil stains require degreasing with appropriate solvents or cleaners. Paint and sealers typically need mechanical removal through grinding or shot blasting. The goal is to expose clean, porous concrete that can form a strong bond with the coating. Previous basement floor paint applications often leave residue that must be completely removed for proper adhesion.
Mechanical Preparation
Most concrete surfaces require mechanical preparation to achieve proper profile. This might involve grinding, shot blasting, or acid etching, depending on the substrate condition and coating requirements. This step is particularly crucial when transitioning from basement floor paint to professional epoxy systems.
The surface profile must match the coating system requirements. Too little profile results in poor adhesion, while excessive profile can consume extra coating material. Most systems specify the appropriate profile range for optimal results, with epoxy indoor floor applications typically requiring more aggressive preparation than basement floor paint.
Moisture Testing
Concrete moisture content can significantly impact coating performance. Excessive moisture can prevent proper curing and lead to coating failure. Several test methods can determine moisture levels, with calcium chloride testing being most common. This is particularly important for epoxy indoor floor applications in basement environments.
Moisture issues must be addressed before coating application. This might involve additional drying time, mechanical ventilation, or moisture barrier systems. Ignoring moisture problems virtually guarantees coating failure, regardless of whether you're using basement floor paint or professional epoxy indoor floor systems.
Basement environments are particularly susceptible to moisture problems due to their below-grade location. Proper moisture testing and remediation are essential for successful epoxy indoor floor installations in these challenging conditions.
What Are the Application Best Practices?
Successful coating application requires attention to detail and adherence to manufacturer specifications. Environmental conditions, mixing procedures, and application techniques all impact final results.
Environmental Conditions
Temperature and humidity must be within specified ranges during application and curing. Most systems require temperatures between 50-80°F with relative humidity below 85%. Extreme conditions can prevent proper curing and lead to coating defects.
Air circulation helps ensure proper curing and reduces solvent retention. Adequate ventilation is particularly important with solvent-based systems, both for performance and safety reasons.
Application Techniques
Application techniques vary by product, but most systems require consistent coverage rates and proper wet-edge maintenance. Working in manageable sections helps ensure uniform appearance and prevents lap marks. This is especially important with floor painting epoxy applications where proper technique directly impacts final appearance.
Understanding the working time of your chosen system is crucial for success. Floor painting epoxy typically offers longer working time than fast-cure alternatives, allowing for better application control and finish quality.
Curing Considerations
Full cure takes time, even after the surface appears dry. Light foot traffic may be possible within 24 hours, but full chemical and mechanical properties develop over several days. Patience during the curing period prevents damage to the new coating.
Temperature affects curing speed, with lower temperatures extending cure times. Planning projects around seasonal conditions helps ensure optimal results.
How Do I Maintain My Coated Floor?
Proper maintenance extends coating life and preserves appearance. Most coated floors require only basic cleaning, but specific procedures help maximize performance and longevity.
Daily Cleaning
Regular sweeping or dust mopping removes abrasive particles that can cause wear. For wet cleaning, use mild detergents and avoid harsh chemicals that might degrade the coating surface.
Spills should be cleaned promptly to prevent staining and potential chemical attack. While most professional coatings resist common chemicals, prolonged exposure to aggressive materials can cause problems.
Periodic Maintenance
Deep cleaning with appropriate cleaners removes accumulated soils and restores surface appearance. The frequency depends on traffic levels and environmental conditions.
Some coatings benefit from periodic recoating of high-traffic areas. This maintenance coating extends system life and maintains appearance with minimal effort compared to complete recoating.
Damage Repair
Minor damage can often be repaired without complete system replacement. Small chips or scratches can be touched up with matching material, while larger areas might require sectional replacement.
The repairability of coated floors is a significant advantage over other flooring options. Most damage can be addressed quickly and economically, extending the overall system life.
What Are Common Application Mistakes to Avoid?
Understanding common mistakes helps ensure project success. Many coating failures result from preventable errors during preparation or application.
Inadequate Surface Preparation
Rushing through surface preparation is the most common cause of coating failure. Proper preparation takes time and effort, but it's essential for long-term success. Attempting to skip preparation steps virtually guarantees problems.
Incorrect Mixing Ratios
Multi-component systems require precise mixing ratios for proper curing. Estimating ratios or using incorrect proportions can result in soft, uncured coatings that never achieve full performance.
Environmental Violations
Applying coatings outside specified temperature and humidity ranges can cause numerous problems. These might include poor adhesion, surface defects, or incomplete curing.
Inadequate Coverage
Applying too little coating material leaves the surface under-protected and may result in early failure. Following manufacturer coverage rate recommendations ensures adequate protection.
How Do Indoor Coatings Compare to Outdoor Systems?
Indoor applications present different challenges and opportunities compared to outdoor installations. Understanding these differences helps optimize system selection and application procedures, particularly when choosing between basement floor paint and professional epoxy indoor floor systems.
Environmental Factors
Indoor environments typically offer more controlled conditions with less temperature variation and no UV exposure. This allows for different chemistry options and generally easier application conditions. Epoxy indoor floor systems benefit from these controlled conditions, achieving better cures and longer service life than similar systems exposed to outdoor elements.
Humidity control is often easier indoors, though basements and other below-grade spaces may present moisture challenges. Understanding the specific indoor environment helps guide system selection. Basement floor paint may seem adequate in controlled conditions, but professional epoxy indoor floor systems provide superior long-term performance even in challenging basement environments.
Performance Requirements
Indoor floors often face different chemical exposures and traffic patterns than outdoor surfaces. Basements might see occasional water exposure, while workshops may encounter oils and solvents. These conditions quickly reveal the limitations of basement floor paint compared to professional epoxy indoor floor systems.
The aesthetic requirements for indoor spaces are often higher than outdoor applications. Appearance retention and cleanability become more important factors in system selection. Professional epoxy indoor floor coatings maintain their appearance far longer than basement floor paint under identical conditions.
Maintenance Considerations
Indoor floors are typically easier to maintain than outdoor surfaces. Protection from weather and UV exposure extends coating life and reduces maintenance requirements. This advantage is particularly pronounced with epoxy indoor floor systems compared to basement floor paint applications.
Accessibility for cleaning and maintenance is usually better indoors, allowing for more frequent care that extends system life. Regular maintenance of epoxy indoor floor systems is minimal compared to the frequent reapplication required with basement floor paint.
Professional epoxy indoor floor systems resist staining and chemical damage far better than basement floor paint, making routine maintenance easier and more effective. The smooth, non-porous surface of cured epoxy systems cleans easily with standard methods.
What Are the Cost Considerations?
Understanding the total cost of ownership helps make informed decisions about coating systems. Initial cost is only one factor in the overall economic picture.
Long-Term Value
Professional coatings typically last 10-20 years or more with proper maintenance, while paint systems may need replacement every 1-2 years. This makes professional systems more economical despite higher initial costs.
The improved appearance and functionality of professional coatings can also increase property values, providing additional return on investment.
Maintenance Costs
Professional coatings require less maintenance than paint systems. The superior durability and cleanability reduce ongoing costs while maintaining appearance.
Repair costs are typically lower for professional systems due to their repairability. Local damage can often be addressed without complete system replacement.
Choose ArmorPoxy!
Professional floor coating systems offer superior performance, durability, and value compared to traditional paint products. Understanding the differences between systems and proper application procedures helps ensure successful results.
ArmorPoxy provides comprehensive solutions for indoor floor coating needs, from basic protection to advanced decorative systems. Our products are designed for professional results while remaining accessible to experienced DIY enthusiasts.
The key to success lies in proper system selection, thorough surface preparation, and careful application procedures. When these factors are properly addressed, professional coating systems provide decades of reliable service while maintaining their appearance and protective properties.
Whether you're upgrading a basement, workshop, or commercial space, investing in professional floor coatings provides lasting value and satisfaction. The superior performance and durability of these systems make them the clear choice for anyone serious about protecting and beautifying their indoor concrete surfaces.